JOB MANAGEMENT DONE IN AN INSTANT
Nowadays, traditional industries must comply with a great deal of challenges and requirements such as high-tech, high-efficiency, sustainability and so on, making it very hard to succeed for those Wire & Cable industries which are reluctant to adapt to new technologies.
How to make good use of the resources in an efficient and flexible manner is going to be a key factor to decide whether a company is going to be competitive or not.
To fulfill that need, Pioneer Machinery brings three SmartFA models that help building digital flows for a traditional factory.
INTRODUCTION
Digital flow is a key factor when talking about smart factories. The connection between OT and IT allows to fetch the information in a more effective manner, helping relevant personnel when it comes to decision making.
The Job Dispatch System comes with a highly customized design. It allows digital management systems to be applied to a cable manufacturer and successfully fulfill the goal of smart manufacturing.
COMMON PROBLEMS
Cable manufacturing is sorted into different stages of continuous production processes, which can be complicated when scheduling and planning. Traditional job dispatch system may confront the following difficulties:
BENEFITS OF A JOB DISPATCH SYSTEM
UI OF PIONEER JOB DISPATCH SYSTEM
BENEFITS OF JOB DISPATCH SYSTEM
100%
work force and time efficiency increase for task delivery.
- Time and amount of person for task delivery by paper: 0.5 person/30 minutes
- ⇩
- direct delivery to the machine without delay and no worker required.
100%
decrease orders lost or corrupted
- percentage of orders lost or corrupted by paper order 1-2 %
- ⇩
- 0% by digital flow orders
91.6%
of time saving on scheduling the order
- For the scale of a factory with 20 lines, it takes around 60 minutes to collect all the data
- ⇩
- with the job dispatch system it only takes 5 minutes.
Introduction of recipe system
becomes key for success.
Parameter input issues
The adjustment of production parameters are related to a wide range of factors and sometimes it becomes nearly impossible to take every single one of them into consideration, so elasticity becomes much more important than it used to be. Traditional parameters setting might confront the following handicaps:
Recipe system features
UI OF Pioneer RECIPE SYSTEM
BENEFITS OF RECIPE SYSTEM
84%
time decrease for parameters setting
- 10-15 minutes ➟ 1-3 minutes
67%
time decrease during production trial run
- 30-90 MINUTES ➟ 10-30 MINUTES
87.5%
decrease on human key-in errors
- 3-5% ➟ <0.5%
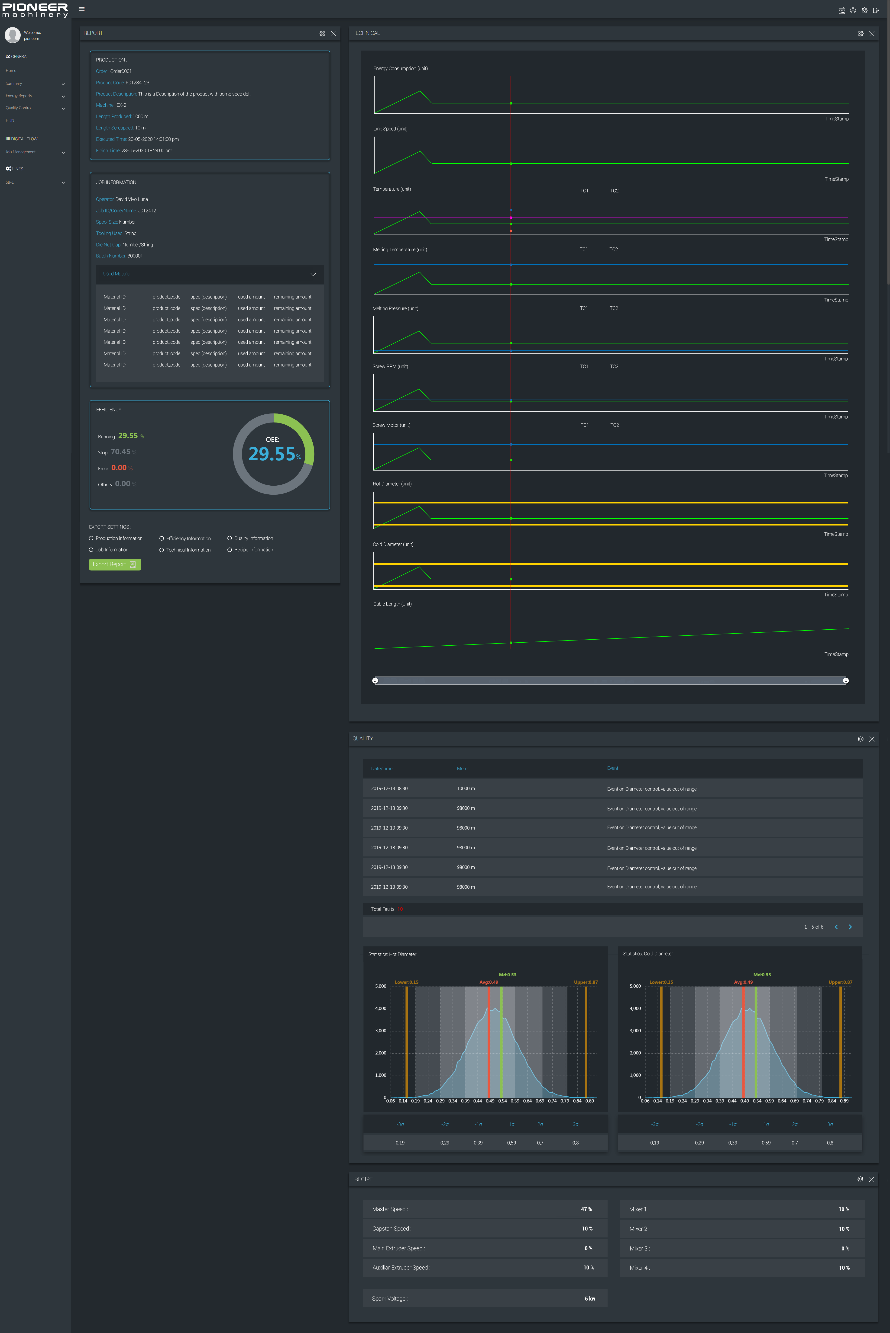
Job Report features
By presenting machine data in a visualized way, with more charts and forms, Job Report is able to output these results effectively and without any delay. Compared to the traditional paperwork, the Job Report system can do a great job on economizing time and decreasing the rate of occurrence of error.
Improving traditional workflow with paper
Manufacturing workflow in the Wire & Cable industry is complicated as it takes more time to record every single detail with paper. With the Job Report system, a factory can record data in a more economical and efficient way.
Job Report is with traceability
Job report allows factories to be able to record every piece of information in the workflow. This information can be later on traced back and revisit whether there was a mistake or error that needs to be solved or if there is any improvement that can be done in their workflow.
Immediate and accurate data
With automatic data collection, the information can be gathered and organized into an exhaustive report in a short period of time. This way we could also avoid delays and errors during parameters keying in.
BENEFITS OF JOB REPORT
Time of recording production data:
- 10-30 minutes➟ Immediate recording in real-time
Time of making a report:
- Immediate report generated in real-time
Reversibility of Job Report:
- Using statistical methods find the correlation between parameters.